here you can see different repair examples:
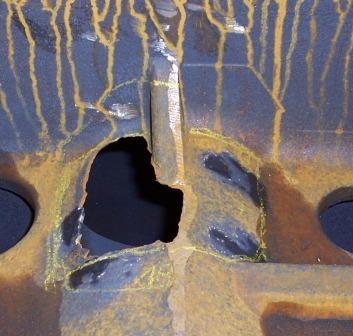
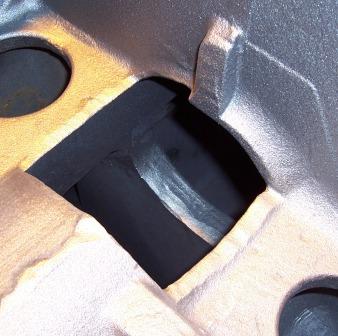
cast thickness not correct founded, faulty material is cuted out.
strut support is not ensured.
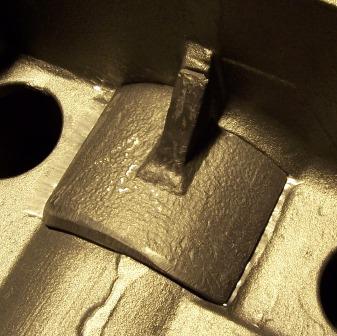 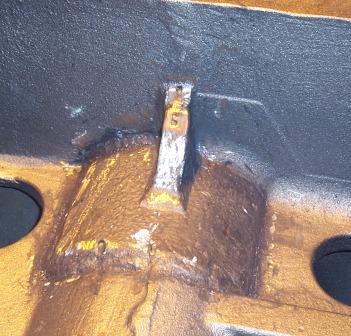
part for set in is prepared, and fixed tight with latch plates and screw mountings.
through the cast thickness from the inserted part, strut support is ensured.
hub of a francis - turbine rotor
on three points cracked.
after the latching treatment,
the bore of the hub was drilled out
and a new turbine shaft adapted.
bearing case of a excenter press the top surface was fixed with a lock bar
cracked through complete. and latch plates.
the side of the bearing case and the inner diameter were fixed with latch plates.
during the treatment, the bearing case was adjusted and fixed on a directional plate.
so it was possible, to achieve the smallest geometricaly difference on the case.
1000 to presses for the production of parts for the automotive industry.
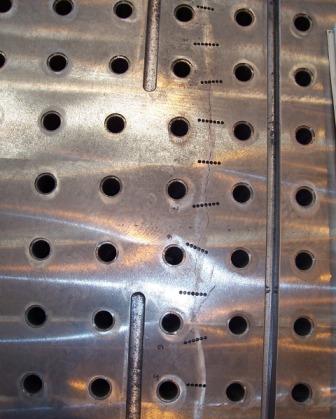
support plate for this presses, with a dead weight from 16 to,
over a length from 2 meters cracked. plate on the upper and lower side repaired.
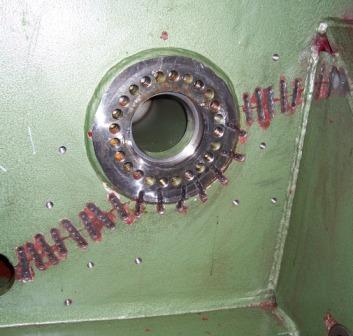 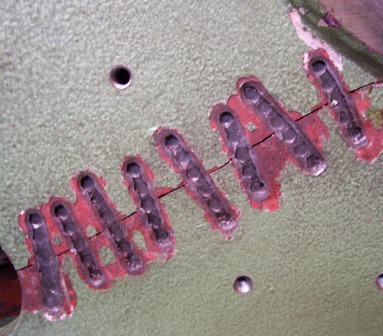
frame of a machine cracked. latch plates caulked.
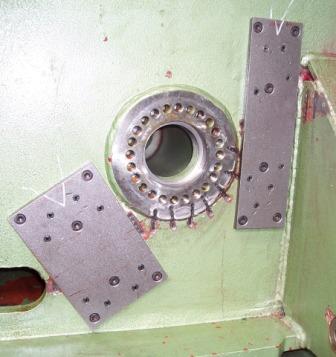
after the repair,
additional for more safety,
support plates are fixed,
demanded of hard pin cutting.
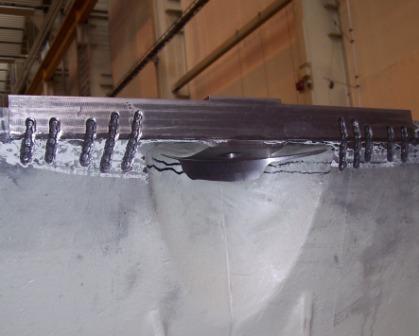 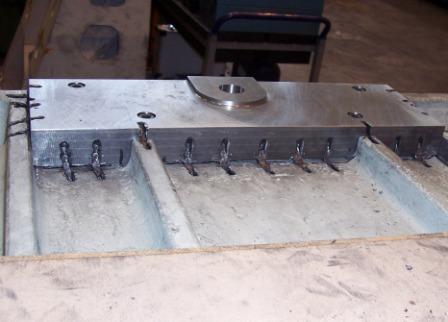
machine bed not correct founded. the faulty material was cuted out and a prepared plate inserted and fixed with latch plates.
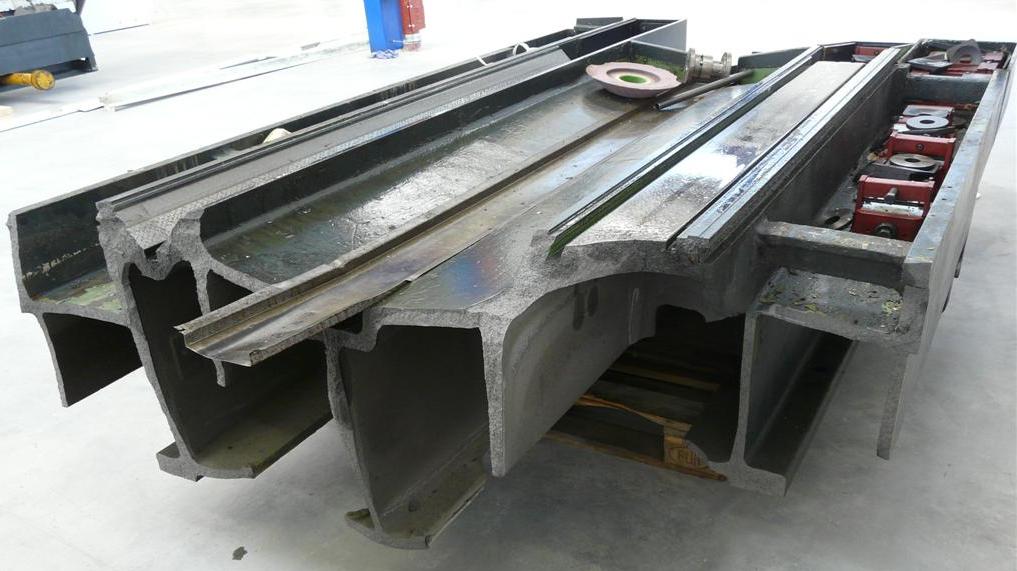
a grinding machine bed with a length of 8 meters and a width of 2 meters.
a part with a length of ca. 2,5 meters was broken off complete.
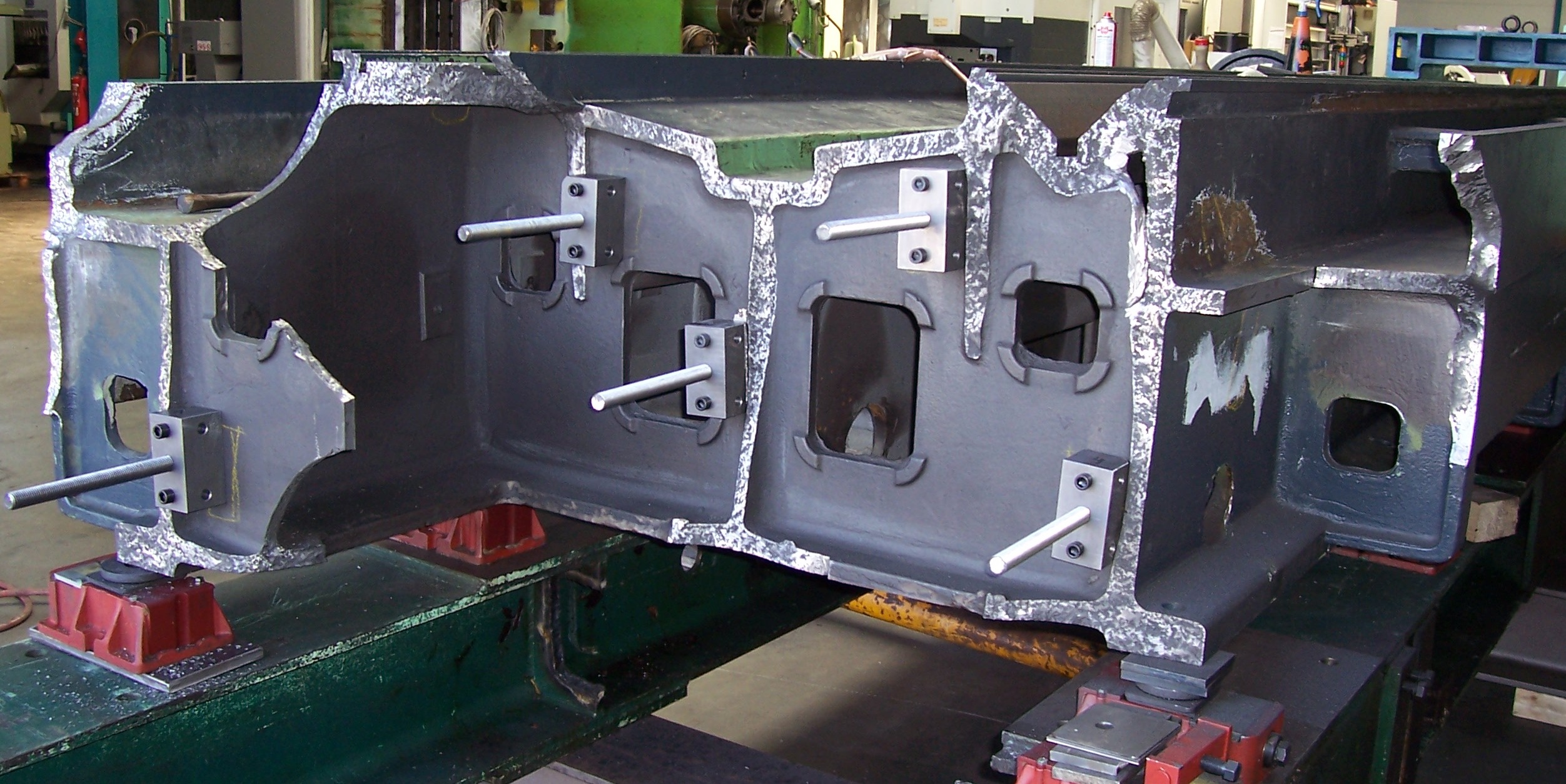
the opposite part during the preparation for the adjusting work.
the necessary tightness and stability should be reached.
also the necessary denseness over the complete width have to be reached.
after the repair, the guidline surfaces should be reworked by grinding.
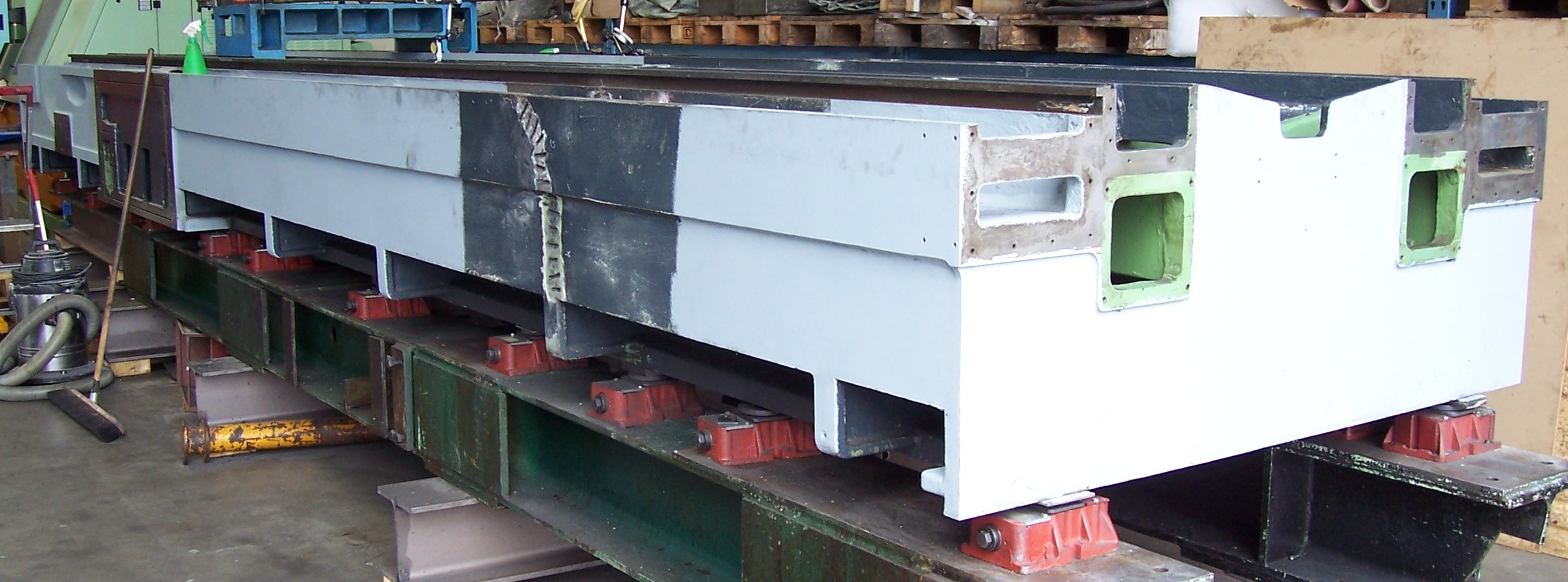
after the latching repair, the machine bed is completed.
the necessary tightness, stability and denseness were reached.
with a very exactly adjusting work on a adjusting bench, the guidline surfaces got an exact machining allowance of 0,3 mm for the regrinding work.
|